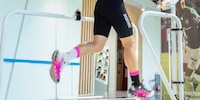
Background information
Why a running analysis was worthwhile for me – and might be something for you too
by Siri Schubert
Global technology company Logitech has its headquarters in Lausanne, Switzerland. A unique aspect of the facility is its Ergo Lab, where Logitech refines products to make them more ergonomic. Here’s my interview with the lab director.
How can we design devices so that they make us productive rather than unwell? In this interview, Agnès Lisowksa Masson, Head of the Ergo Lab at Logitech, reveals why even holding your head in a slightly tilted position can be problematic, and how sensors help create the perfect computer mouse.
Your exact job title is «Human-Computer Interface Specialist & Scientific Lead of the Ergo Lab». What does that entail?
Agnès: I study the way people use technology and how we can design tech to serve people and not the other way around. If you think back to the early days of computers, everything was developed on the basis of how machines work. Human beings had to adapt to that. Today, technology is so advanced that the opposite should be the case.
How did you get into this field?
I come from a family of engineers, so being interesting in technology was pretty much in my blood. At the same time, I’ve always been fascinated by how people work. Or more precisely, how our brains work, what makes us tick and why we behave in certain ways.
It’s the interface between technology and human behaviour that drives me.
Can you expand on that with an example?
A brilliant device, such as a notebook, is fine for work. However, it takes more than that to enable a user to work in a healthy way; the entire setup has to be considered. It’s easy to explain this. Your head weighs about six kilogrammes. When it’s perfectly aligned over your spine, your neck and shoulders can easily support that weight. However, when your notebook’s on your desk, your head’s tilted at an angle of ten to 15 degrees. That doesn’t sound like much, but once gravity’s factored in, your muscles have to work harder to hold the equivalent of 12 kilogrammes. This can cause discomfort.
A simple solution to this is to raise your notebook. You can also use an external mouse and keyboard to adjust the position of your wrists. This gives you a natural, comfortable posture when you’re working for long periods.
How do you translate this knowledge into specific products, such as the Lift computer mouse?
In our lab, we attach sensors to volunteers to find out how certain devices affect them. In the case of mice such as the Lift, we use sensors for muscle activity and posture. Muscle sensors tell us how much strain is being placed on a person’s muscles while they’re using a mouse. If the mouse is too small, for example, we see a high level of thumb activity. Switching to a larger mouse reduces this strain. A trackball mouse doesn’t put any more strain on the thumb muscles than a regular mouse.
What do you monitor using posture sensors?
We attach these to body parts such as the wrist or neck to monitor the alignment of the skeleton. These sensors can determine whether ergonomic products such as vertical mice are doing their job. They’re designed to position your arm in a more natural way, reducing the risk of muscle tension. Another thing they do is allow us to determine the ideal angle.
What else do you measure?
We use pressure sensors to ascertain how much pressure’s being put on a work surface. They measure the way products like keyboards and wrist rests distribute weight and pressure so that we can make sure they’re providing the right support. Choosing to use softer or firmer materials can have a significant impact on a product’s comfort and ergonomics.
Thermal imaging cameras give us additional information. They reveal the hand’s points of contact on different devices, helping us understand how different people grip their devices. Not only that, but they reveal unwanted contact points at corners and on buttons. For instance, if a button’s so close to the spot where someone’s gripping the mouse that they accidentally press it. This type of feedback is crucial when you’re developing user-friendly products.
At what point in a product’s development does your work begin?
We work very closely with product managers, designers and other employees right from the start. You can’t retrofit ergonomic features – and you have to bear that in mind from the outset.
Once our design team has an initial outline, we actually test it in the early stages. We start with block models, optimising the design by adjusting angles, curves and other details to ensure that the user’s hand, for instance, can rest as naturally as possible. This allows us to quickly determine whether there’s actually a benefit.
Our aim is to find the happy medium between ergonomic benefits, performance and aesthetics.
What considerations do you focus on at that stage?
We figure out what restricts people at work. That’s what results in the best products. It might be something seemingly trivial, such as how people position their wrists when typing. Holding them flat on a keyboard is unnatural, so a product would emerge from the idea of improving this posture.
How do you know about these restrictions?
There’s a lot of scientific literature on ergonomics that we use as a reference point.
How long do your tests last?
The tests are usually carried out for a short time. We can see relatively quickly if something isn’t suitable. Long-term tests are tricky because people do other things besides just typing on a keyboard. There are a number of factors that can affect comfort or discomfort.
How is that discomfort expressed?
Sometimes, people just tell us that something’s unpleasant. Other times, we see it when we’re processing data from muscle activity and posture sensors. If the muscle activity recorded with prototype A is too high or higher than with prototype B, then prototype B is probably the better option. We always combine subjective feedback with objective sensor data, which gives us different perspectives.
Speaking of different perspectives, how do you put together the ideal test group?
We always test mice and keyboards on people with different hand sizes: small, medium and large. What’s more, we make sure to run tests with people of different genders and, depending on the product, different skill levels.
At least 20 people take part in each test, as that’s the minimum we need to do a statistical analysis and get reliable data. Depending on how many iterations a product goes through, over 100 people might take part. However, that number isn’t fixed – it varies depending on the context we’re looking at.
What do you like best about this process?
I love seeing how people react to new products. I’m interested in seeing different perspectives and how people approach a product. You gain insight that you never would’ve come upon yourself.
A kind of collective knowledge flows into the development of these products – not just the team’s expertise.
And what are you less keen on?
To be honest, nothing. My work is genuinely interesting. Even when minor difficulties crop up, they get overshadowed by all the good things.
To wrap up, can you give us any tips on improving ergonomics at work?
Even small changes can lead to major improvements. So you don’t have to turn your entire workspace upside down. If, say, a chair isn’t ergonomic, even just placing a cushion in the back can serve as makeshift lumbar support. Or even simpler: take a five to ten minute break every hour. This helps keeps you physically and mentally on point.
Ergonomics is about adapting a workstation to an individual. There’s no one-size-fits-all solution – it’s about finding out what feels right. Small, gradual changes add up to positive results over time.
From big data to big brother, Cyborgs to Sci-Fi. All aspects of technology and society fascinate me.